E-commerce Shipping Damage Control
If someone approached you and asked: “How do you undertake shipping damage control for your e-commerce business?” Would you be able to provide a detailed response, or would every instance of damage flash before your eyes? Today, we’ll talk about shipping damage control in an e-commerce company and how to prevent it.
Appropriate Box Sizing
The first step in managing shipping damage control is determining suitable box sizes for your products. As an e-commerce business, it’s your responsibility to ensure the items your consumer purchases arrive safely and in great condition. While it may seem like a good idea to have space in between multiple items within a shipment – it’s not. Allowing additional space within a package increases the likelihood of damage throughout the product’s journey. You can package your items tightly by downsizing your packing methods based on what products customers order. This decreases the chance of being knocked around, bent, or otherwise damaged throughout the delivery process.
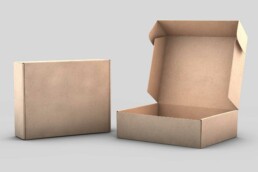
Appropriate Package Filler
Using the right type and amount of filler is equally important to package size. Although packing filler varies by product, using common practices will lead you in the right direction. Glass, for example, should be wrapped in bubble wrap and carefully put in a box of appropriate size. Objects that are less fragile should be packed together using plastics or paper to fill extra space. Keeping each component in place with proper filler and package size reduces the chance of damage.
Improper Handling Procedures
There are many things that can go wrong when handling products and shipments. Poor handling in-house often causes the majority of damages. Processing starts when the manufacturer delivers your products, and concludes when products are delivered to customers. There are many things that can go wrong while items are in inventory. Stacking pallets, loose items, lack of space, and disregarded safety measures are examples of situations that ultimately lead to an accident or a ruined product. Keeping your warehouse and inventory organized reduces the risk of product damage.
Did you know Falcon’s fulfillment team checks for product damages twice?
Manufacturer Damages
Sometimes shipments coming directly from your manufacturer may arrive damaged. Although this may be aggravating, there are steps you can take to prevent damage. Whether your fulfillment process is in-house or via a 3PL partner, it is critical to do quality checks on each and every delivery. This will ensure no damaged items are stocked into inventory and allow notification of reoccurring issues. To have the problem fixed, contact your manufacturer when quality inspections are complete and mistakes are discovered. By frequently communicating with your manufacturer, you can reduce the likelihood of receiving damaged items.
Moisture & Heat Damage
Conventional packing materials do not prevent the long-term harm that temperatures may inflict. That’s why it’s critical to take charge of your inventory conditions before they become an issue. It’s essential to ensure that the area in which your items are stored, is constantly kept cool and dry whether working in-house or with a 3PL fulfillment partner, allowing products to sit under a window, where they may absorb heat and sunshine, may cause damage in the long run.
If your inventory area is damp, your items may become damaged, wet, torn, or worse over time. Keeping your facilities clean, dry, and cool will help in avoiding numerous shipping damage control setbacks.
Falcon keeps warehouse temperatures between 50 and 70 degrees to keep product quality high.
Pest Contagions
It’s important to take measures against pests before they become an issue. Spraying for insects and other pests on a regular basis helps to keep your facilities clean and pest-free. As an added precaution, inspect your inventory for signs of pests on a regular basis. Chewed or torn boxes, rodent droppings, frequent insect sightings, nests, webs, and even faint sounds may all be indicators of pests. Once identified, problems may be rectified in order to prevent an infestation from developing.
COVID-19 Sanitation Procedures
COVID-19 has brought out new sanitary measures and new procedure standards. A customer’s purchase goes through many hands before it reaches their door. It is more vital than ever to ensure that all orders, products, and shipments are properly sterilized and safe for delivery. Contact your manufacturer and 3PL to ensure that the product is subject to sanitation measures prior to arriving at your inventory facility. So, when orders arrive, they are safe and ready for customers to enjoy.
Shipping Damage Control Via Carriers
Damages caused by shipping carriers are a leading concern for e-commerce businesses. Even if you follow every shipping damage control procedure, and ensure orders have left your facility basically perfect – it still doesn’t promise a perfect arrival at your customer’s door. Here are a few tips you can use to protect your items from shipping carrier damages.
Follow Packaging Guidelines for Shipping Damage Control
Packing your orders correctly is one of the best methods to ensure they arrive at your customer’s door safely. Remember when we spoke about proper box sizes and snug-fit packaging filler? Box your orders properly and you’ll have little to no room for items to move, break, or bruise.
Fragile Labeling
Another way you can add additional precautions to the safety of your packages is by adding “fragile” or “handle with care” labels to each order. This will ensure that shipping carriers do just that and apply extra care to your packages. Now, this isn’t a fool-proof way of guaranteeing the safety of your shipments, but it does offer a visual precaution for considerate carrier staff.
Review Carrier Analytics to Resolve Issues for Shipping Damage Control
If all else fails and you find that your orders continuously arrive damaged to your customer, simply go over your shipping analytics. By finding which carrier to responsible for the most damage, you can contact them and discuss your concerns, or simply cut them off altogether.
Beginner’s Guide to Third-Party Logistics (3PL)
The world of e-commerce is always changing, therefore understanding the roll of Third-Party Logistics is integral to keeping up. In light of this our beginner’s guide to third-party logistics (3PL) will delve into the essential aspects, offering insights into fulfillment services, warehousing, and much more.
Read More…
Let Falcon Fulfillment Handle Your Shipping Damage Control
Let the pros at Falcon Fulfillment handle your damage control. That way, you’re free to master other important topics such as eco-friendly packaging or your company’s inventory management system success.
Everything Included in Shipping Damage Control and More
At Falcon Fulfillment, you’ll receive top-quality standards for everything listed above. This includes proper packaging, waste reductions, proper handling protocols, manufacturer communication, inventory sanitation, temperature control, pest precautions, FDA-certified distribution centers, and approved COVID-19 sanitation procedures. Learn more about working with Falcon. Everything we’ve talked about today – is what we do every day. By working with Falcon Fulfillment, you get to transfer the weight of fulfillment from your shoulders to ours, giving you the freedom to grow in other areas of your business.