Inbound and Outbound Logistics
Logistics coordinates and moves resources – people, materials, inventory, and equipment – from one location to storage at the desired destination. It is the process of doing this. Regarding e-commerce, logistics management involves a significant aspect of business operations. Furthermore, logistics is a considerable expense, with businesses spending more than $1.64 trillion on logistics-related activities last year alone. What are the main differences between inbound and outbound logistics? What are the main challenges, and how can streamlining logistics benefit your business? This text and more will cover all this, read on!
Inbound vs. Outbound Logistics
Inbound logistics refers to where goods and materials enter the supply chain to sell to the customer. Outbound logistics refers to the process where the company sells and delivers the finished products to the customer. Streamlining both aspects of logistics is crucial to the company’s profitability and success.
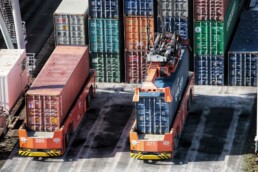
What is outbound logistics?
Outbound logistics involves storing and moving goods to the customer or end user. Outbound logistics includes the systems required to prepare, pack, and deliver packages. The steps include order fulfillment, packing, shipping, and customer service related to delivery.
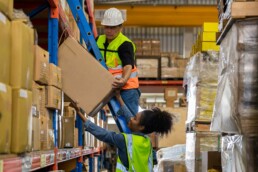
Warehousing
In order to meet customer demands, an e-commerce business needs a warehouse or storage facility to store surplus inventory. The US Business Inventory/Sales Ratio is 1.33, up from 1.26 last year. You can store your inventory in your own warehouse or partner with a third-party provider. Warehousing is a significant expense for e-commerce businesses. Whether you outsource your warehouse needs or handle them in-house, it is a crucial part of outbound logistics.
Inventory Management
Most e-commerce companies use inventory management software to maintain a consistent flow of orders and sales. Inventory management involves carrying adequate levels of stock to fulfill customer orders. It is a vital part of business management because it allows companies to boost profits and reduce overhead. There are many benefits to employing an automated inventory management system, including improved accuracy and better transparency. Inventory management also includes:
- Product locations
- Quantities of each product type
- Profit margin by style, model, product line, or item
- Setting the ideal amount of inventory to have in back stock and storage
- How many products to reorder and how often
- When to discontinue a product
Streamlined inventory management can boost profitability and improve customer experience. It allows you to capture and fulfill every sale while simultaneously avoiding overstock.
Order Processing
When a customer orders through the sales channel, a notification is sent to the warehouse for fulfillment. The staff in the warehouse receives the order and verifies its validity. They ensure the product(s) are in stock and can be made ready to send out to the customer.
Picking, Packing, and Kitting
All items are packaged, sealed, and labeled for shipment at this stage. Once an order is received and verified, the order has to be carefully picked, packed, and prepped for transport. Some items or orders, like subscription boxes, also require kitting services, where more than one product is carefully assembled into one shipment or package.
Transportation
Transportation involves any method or mode to move goods from your storage warehouse to a carrier distribution center or direct-to-customer. When moving goods to a distribution center or fulfillment facility, larger vehicles like freight carriers, semi-trucks, and rail lines are used. Then products are separated into smaller vans or vehicles to be delivered to the end consumer.
Last Mile Delivery
The final aspect of outbound logistics is the last-mile delivery to the end customer. Whether the package is delivered to a home or office, this is the culmination of the logistics journey. If the final delivery is unsuccessful or the product arrives damaged, the product may be returned, triggering an inbound logistics process (returns).
What is inbound logistics?
Inbound logistics is when a company secures raw materials, goods, and supplies to produce products it will sell to an end consumer. It is the receiving or incoming part of the supply chain cycle. A few of the critical components of inbound logistics include:
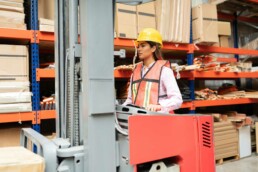
Sourcing and Purchasing
Inbound logistics starts with identifying the materials, goods, or supplies needed to build your product. Next, research potential manufacturers or suppliers of those goods or materials. Once you’ve identified suitable partners, engage with them directly to purchase and receive the materials. Maintain accurate records from purchase orders to ensure smooth reconciliation with shipments.
Transportation
When a manufacturer/vendor ships goods, they provide a notification. This notification includes a tracking number, which helps warehouse and distribution teams prepare for the efficient receipt of the items.
Receiving
First and foremost, this part of inbound logistics involves receiving shipments at the warehouse or distribution center. Loading dock staff then evaluate the shipment for damages and accuracy. Once the shipment is approved, the goods are stored in a designated storage facility or moved to a secondary manufacturing or assembly area. Finally, all goods ready for customer sales are input into the inventory management system and stored carefully.
Each step plays a crucial role in ensuring the smooth flow of goods and materials throughout the organization. Receiving shipments efficiently and accurately is essential for maintaining optimal inventory levels and meeting customer demand.
Reverse Logistics
The final aspect of inbound logistics occurs after a sale. Reverse logistics includes adding products back into the supply chain due to a product return. Check out 4 Ways to Streamline Returns Management.
Challenges of Inbound and Outbound Logistics
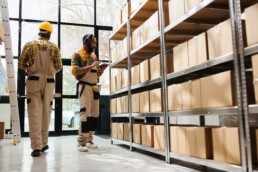
Inbound logistics challenges
The main challenges of inbound logistics include the following:
- Finding reliable and trustworthy suppliers
- Sourcing affordable suppliers and manufacturers
- Balancing inflow and outflow of goods to maintain adequate materials without overstocking
- Managing transportation delays and boosting supply chain resilience
- Maintaining receiving and quality control processes
Outbound logistics challenges
The main challenges of outbound logistics include the following:
- Hiring quality staff to manage order processing
- Maintain order accuracy and efficiency
- Negotiating transportation and shipping contracts to keep costs low
- Meeting delivery timeline expectations
- Reverse logistics management and process
Benefits of optimizing logistics
Inbound and outbound logistics are necessary for business operations to run smoothly. Without products, there are no sales, and vice versa without sales. Therefore, inbound and outbound logistics must work together for optimum success. This text provides some ideas to optimize your logistics process.
Maintain optimal inventory levels
Having too much or too little inventory is not ideal. If you order too much inventory, then you risk paying high storage fees. If you order too little, you miss out on sales opportunities and risk disappointing customers. To maintain optimal inventory levels, you need to commit to regular inventory audits, offload slow-moving stock or deadstock, invest in items with higher turnover rates, and those products with higher margins. Successful companies regularly review demand forecasts and take physical stock counts. Striking the correct inventory levels will reduce overhead costs from storage, improve product performance and profitability, and improve procurement workflows.
Improve warehouse management
Implementing a streamlined warehouse management process reduces human error and will improve order accuracy, shipping efficiency and maximize storage utilization. Most companies use software programs that help to automate inventory levels, trigger reordering events, automate picklist creation, and track shipment deliveries.
Beginner’s Guide to Third-Party Logistics (3PL)
The world of e-commerce is always changing, understanding the roll of Third-Party Logistics is integral to keeping up. This beginner’s guide to third-party logistics (3PL) will delve into the essential aspects, offering insights into fulfillment services, warehousing, and much more.
Read More…
Partner with a 3PL to optimize logistics
If you spend more than 15% of your time managing your logistics, it might be time to investigate working with a 3PL. 3PLs partner with e-commerce businesses as experts who handle inbound and outbound logistics. They manage receiving, warehousing, negotiating with shipping carriers, and returns. Some 3PLs, like Falcon Fulfillment, can provide flexible inventory storage in their fulfillment centers.