How to Create an Effective Reverse Logistics Plan
Any successful streamlined supply chain relies heavily on reverse logistics. Consumers have grown to expect an easy return policies and processes. Creating an effective reverse logistics plan can increase sales, customer satisfaction, and loyalty. Let’s look at what reverse logistics is and how to create an effective plan.
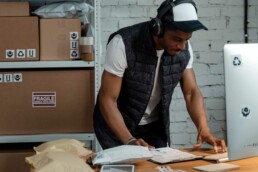
What is reverse logistics?
Reverse logistics is a type of supply chain management that moves goods from customers back to businesses responsible for selling or creating them. Simply put, reverse logistics deliver goods from the customer back to the manufacturer or seller. Returns are the most common; however, reverse logistics can include refurbishing, unsold seasonal goods, delivery failure, and repairs or maintenance.
How does reverse logistics work?
The reverse logistics process begins after the sale of a product. Typically, a customer or vendor initiates it when they are dissatisfied with a product or no longer find it useful. The steps required for a return to be successful will vary greatly by industry. Depending on the industry and product, the responsible party will arrange for the transportation of the item back through the supply chain. This includes sending return labels, packing materials if necessary, or scheduling a local pickup for larger or bulky items.
Why create a reverse logistics plan?
A reverse logistics plan can reduce storage and distribution costs. It can improve customer relationships, retention, and satisfaction and create a sustainable supply chain. Some companies are starting to leverage their return policies as a competitive advantage. Let’s get into the components and best practices of an effective reverse logistics plan.
Components of creating an effective reverse logistics plan.
Returns Management
Returns management is the area of business operations that oversees inbound product returns. An effective plan will leverage methods that ensure speed, visibility, and control. This includes; implementing technology for automated returns, inventory tracking, restocking, and disposing of products ineligible for resale. Building an effective returns process can help a company reduce, reuse, and recycle materials that otherwise would end up in a landfill, thus boosting a company’s sustainability efforts. Not only that, but managing returns will help to increase profitability by minimizing inventory costs.
Return Policy and Procedure
A return policy or procedure are the rules that a retailer outlines when a customer needs to return or exchange a product for any reason. The bare minimum included in a return policy is the type of products that can be returned, acceptable reasons for a return, and the timeframe in which a return needs to be actioned. It is crucial to develop a fair and balanced return policy because this helps build trust between a brand and the consumer. Vital elements of a great returns policy are as follows:
- Clear communication
- Hassle-free
- Costs are fair (e.g., don’t make the customer pay for return shipping if the item arrived damaged)
- Flexible (if a customer is one day over the timeframe, make an exception)
- Quickly refund money when necessary
Refurbishment
Another part of creating an effective reverse logistics plan could involve refurbishing products. Depending on industry-specific compliance, many returned products can simply be re-added to inventory for resale. However, there are times when a return is salvageable but must be refurbished or remanufactured. When done well, a solid refurbishment process helps a company recoup financial losses from a return. Additionally, refurbished goods help protect the environment from needless waste.
Unsold Goods
What to do with seasonal or unsold merchandise? Consumers expect brands to dispose of their inventory in a socially responsible way. Big brands that are in the habit of simply trashing their unsold goods are beginning to be called out by dumpster diving activists. Consumers expect brands to dispose of their inventory in an environmentally conscious way. There are a few crafty ideas to help eliminate unsold inventory and minimize the environmental impact of returns.
End-of-Life (EOL)
>While a vintage t-shirt may not have an end-of-life cycle, technology certainly does. Many companies prepare thoroughly for the initial life-cycle stages, including introducing new products, upgrading features, upselling accessories, etc. However, few companies adequately prepare for a product to be phased out. Depending on what products your company sells will determine if an EOL procedure should be included in your reverse logistics plan. Here are a few things to consider if your product does have an EOL cycle;
- Develop an in-depth strategy for sunsetting the product
- Monitor component production for parts that are critical for the product (e.g., Tesla’s battery replacement)
- Communicate with customers early and often if a product will no longer be serviced or available
- Develop a plan to dispose of EOL products responsibly
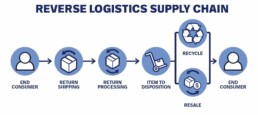
Steps to create an effective reverse logistics plan.
Receive, acknowledge, and process the return.
The first element of reverse logistics is when a customer wants to return a product. Outline a clear way for the customer to begin this process in your returns policy. Once the return has been initiated, it is essential to acknowledge the request has been received. Next is processing the return. Processing a return should include the following:
- return authorization
- scheduling return shipments
- sending package labels if necessary
- receiving returned items
- evaluation of product condition<
- issuing refund
- Shipping an exchange or replacement
Handle returned goods.
Once the returns process begins, it will reach the processing center, where the next step involves categorization. Specifically, the item will undergo options such as being fixed, resold as new, resold as a return, recycled, scrapped, or refurbished. A fully optimized reverse logistics plan will complete categorization before the item arrives at the processing center.
Move returns forward.
Each item, based on its category, requires movement or dispatch to the relevant department. For example, the department responsible for repairs should handle items in need of repair. Similarly, products suitable for resale as new should be reintegrated into the inventory and stored for resale. Often, the returns department can become overcrowded with products waiting for relocation. Managing returns promptly helps businesses prevent inventory level errors and recapture lost revenue.
Repair or refurbish items.
If a returned product is repairable, deliver it to the respective department. For products deemed unsuitable for repair, consider dismantling and selling them for parts. After rebuilding or refurbishing the item, add it to the relevant inventory category.
Recycle
Companies that focus on recycling are doing their part in creating a sustainable future and will be ahead of the curve. Recycle any goods that do not meet the standards for repair, refurbishment, or resale. Locate a recycling partner for products that are unsuitable for resale.
Dispose of unusable products.
Ideally, maintaining a small size for this category relies on carefully following each of the previous steps. Moreover, it remains imperative to execute the disposal of unusable products with consideration for social and environmental impact. Additionally, when other options exhaust, discarding returned products becomes necessary.
Beginner’s Guide to Third-Party Logistics (3PL)
The world of e-commerce is always changing, therefore understanding the roll of Third-Party Logistics is integral to keeping up. In light of this our beginner’s guide to third-party logistics (3PL) will delve into the essential aspects, offering insights into fulfillment services, warehousing, and much more.
Read More…
Every business we have a unique approach to reverse logistics. The product type, industry, and even timeframe will determine which areas of the reverse logistics plan need detailed insights. Regardless, successful companies create effective reverse logistics plans before they attempt to make their first sale. They understand that returns happen, and the more seamless the process, the happier their customers will be. Get in touch today to learn more about how Falcon Fulfillment can help you manage your reverse logistics process.