Calculate Safety Stock Levels for Efficient Inventory Levels
Inventory management is an important part of running a successful business. A key goal of inventory management is having enough stock to meet customer demand while avoiding excessive inventory buildup. Revenue lost due to stockouts from customers purchasing from competitors and the knock-on effect of reduced supply chain efficiency cannot be underestimated. To help manage your inventory levels correctly managed, it’s vital to calculate safety stock for optimal inventory levels. While common, even desirable, to run low on supply due to increased sales, it is also vitally important to calculate accurate safety stock and reorder cadence to ensure the appropriate amounts of product to keep on hand. In this post we will explore how to calculate safety stock for optimal inventory levels.
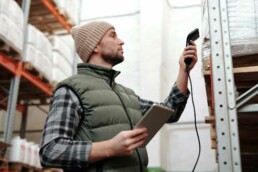
What is safety stock?
Safety stock is a buffer of inventory kept on hand as an insurance policy to protect against unexpected disruptions in supply or demand. It is essential because it ensures that the company can always fulfill customer orders, even when there are unforeseen delays in receiving goods or a sudden spike in demand. Safety stock also reduces the likelihood of stockouts, which can lead to a loss of sales and customer dissatisfaction.
Stockout Effects
Stockouts result in $984 billion worth of lost sales worldwide, with North American companies alone losing $144.9 billion, according to a study by IHL Group. In addition to preventing stockouts, having safety stock on hand can help a business stay competitive by allowing them to respond quickly to changes in the market and leverage last-minute sales promotions.
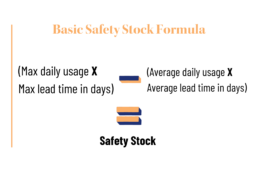
Remember that this formula doesn’t consider dramatic fluctuations in lead time or supply chain bottlenecks. Furthermore, it doesn’t account for customer demand fluctuations or seasonal changes. If you need a more accurate safety stock calculation considering these variables, please check out the following methods.
- Heizer and Render’s Formula – this method is best if you have significantly varied lead times.
- Greasley’s Formula – this method takes into account both lead time and demand fluctuations.
For an extensive deep dive into more techniques to calculate safety stock for optimal inventory levels, check out this post by ABC Supply Chain. They even offer an excel based safety stock calculator.
Safety stock is an integral part of inventory management and ensures optimal inventory levels when regularly monitored. By calculating safety stock levels for each product, you can ensure that your inventory management is effective and that customer demand is met without excessive inventory buildup. Whether you choose the basic method or a more complex formula, having adequate safety stock is good for business.
Beginner’s Guide to Third-Party Logistics (3PL)
The world of e-commerce is always changing, therefore understanding the roll of Third-Party Logistics is integral to keeping up. In light of this our beginner’s guide to third-party logistics (3PL) will delve into the essential aspects, offering insights into fulfillment services, warehousing, and much more.
Read More…
How working with a 3PL can improve safety stock management.
Working with a 3PL can help with safety stock by allowing the 3PL to manage the inventory levels and identify potential future needs. 3PLs are experts in inventory management and can ensure businesses always have the right amount of stock on hand. A quality 3PL can also help with quality control, supply chain management, and flexible storage options. Furthermore, they can provide real-time inventory tracking and reporting so businesses can monitor their safety stock levels and make adjustments as necessary.