Types of Fulfillment Costs
Fulfillment costs are any fees associated with storing inventory, processing orders, and delivering products to the end consumer. They include reverse logistics (returns processing), restocking fees, pick and pack, kitting, and receiving costs. Furthermore, fulfillment costs vary based on the company and the products being sold. Managing fulfillment in-house can be costly and time-consuming. It is crucial to be completely aware of all costs to maximize profitability and accurately calculate ROI. This article will focus on the ten types of fulfillment costs typically charged when working with a 3PL.
Initial Setup
Working with a 3PL involves taking the first step in the initial setup. Subsequently, this process requires integrating your point-of-sale systems with their fulfillment software, inventory tracking, and order tracking programs. Furthermore, most 3PL companies typically charge a flat fee for this service and offer initial training. Falcon Fulfillment, notably, assigns a designated account manager to assist with the initial setup and throughout the relationship.
Account Management
The account management fees cover the administrative costs of handling your order fulfillment. Additionally, this includes customer service fees, technical support, and other ancillary activities aimed at serving your business and clients.
Inbound Shipping
Inbound shipping is the cost of shipping your product to the fulfillment warehouse. Products can ship via land, air, sea, or a combination, depending on the location of the supplier or manufacturer.
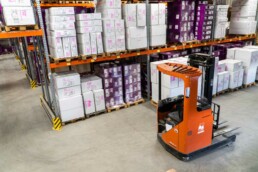
Receiving Cost
Receiving costs, also sometimes called intake fees, include every aspect of processing your product when it arrives. 3PL companies charge by the hour or flat rate (by the unit/item quantity). When your shipment arrives at the warehouse, the staff will review your order for accuracy in quantity and check for damages. Lastly, the receiving crew will scan your inventory into the system, so they are available to be sold.
Inventory Storage
Whether you fulfill in-house or partner with a 3PL, storing inventory involves a cost. You calculate paying for warehouse space based on the size and quantity of the products one stores. Additionally, most fulfillment companies charge additional fees for large, irregular, or bulky items that require special equipment. The notable benefit of working with a 3PL for your inventory storage needs is that, typically, you have flexibility in how much storage you use. This flexibility enables you to scale up or down based on your storage needs for seasonal sales or one-off promotions without being held to a long-term lease.

Pick-n-Pack
Picking and packing orders is another service that many 3PL fulfillment companies provide. After an order is placed, the notification is sent to your fulfillment partner. Subsequently, a staff member selects the items from inventory storage and packages them for shipping. Typically, costs are connected to the type and number of items, as well as whether any special care is required for shipping.
Packaging
Inbound shipping arrives in bulk. Therefore, someone repackages individual products for individual resale. The total packaging cost depends on size, the number of items, box dimensions, dunnage required, and whether one uses standard or custom packaging.
Kitting and Item Assembly
Some orders require light assembly or what one knows as kitting. Kitting refers to a process where one packages and ships individual but related products together as a single product. This is where a product may contain several components to complete a set. Think about things like furniture or small appliances. While they arrive in a flat shipping box, they must be put together at home to function properly. Another example of things requiring kitting or assembly would be product bundles or subscription boxes.
Outbound Shipping
Fulfillment costs typically include high outbound shipping costs. 3PL companies can offer some of the most cost-effective shipping options because they extend their high-volume discounts to their clients. However, outbound shipping costs constantly fluctuate with fuel costs, seasons, and supply chain delays. Calculating shipping costs involves complexity. The calculations include variations based on dimensions, weight, speed of delivery, distance from the distribution center, and special instructions. Partnering with a multi-site 3PL can help clients minimize shipping costs and maximize shipping speed.
Return Management Costs
Only some fulfillment companies offer a returns management service, but it is a valuable and desirable amenity when considering types of fulfillment costs. Managing your customer’s unwanted or damaged goods requires good customer support. In addition, return management costs handle restocking inventory and adding it back into the inventory management system.
Beginner’s Guide to Third-Party Logistics (3PL)
The world of e-commerce is always changing, therefore understanding the roll of Third-Party Logistics is integral to keeping up. In light of this our beginner’s guide to third-party logistics (3PL) will delve into the essential aspects, offering insights into fulfillment services, warehousing, and much more.
Read More…
There is not a one size fits all pricing model for order fulfillment. There are several crucial types of fulfillment costs, such as inbound shipping, storage, inventory management, and outbound shipping. No matter how you plan to fulfill orders, these will be costs accrued. Calculating fulfillment costs can be confusing and complex, and not every 3PL is created equal. Falcon Fulfillment offers a high-quality “White-glove Fulfillment” experience.